
Non-destructive testing of rails and welds
Monitoring and testing technology
Manual testing of rails and welded rail connections
Mechanized rail testing by means of removable trolleys
Mobile rail inspection equipment for rapid continuous testing
The strength and reliability of rails during their operation is crucial for the railway industry. This is connected to the fact that the development of defects and violations of the strength characteristics of the rails may lead to their breaking or even to railway crashes. Long-term operation of rails showed which defects were mainly developing (see UIC Code 712 R) and, of course, this may seriously affect the safety of the railway transportation. The scientific and industrial enterprises which provide in-service non-destructive rail testing constantly improve both the testing methods and the inspection results analysis technology to ensure timely detection of not only critical defects, but also defects that have started their development.
For this purpose, the research and production company OKOndt GROUP has developed a series of ultrasonic and eddy-current rail flaw detectors.
Ultrasonic flaw detectors:
- OKOSCAN 73HS high-speed rails testing system
- single-rail ultrasonic flaw detector UDS2-77
- double-rail ultrasonic flaw detector UDS2-73
- ultrasonic flaw detector Sonocon B
Eddy-current flaw detectors:
Monitoring and testing technology
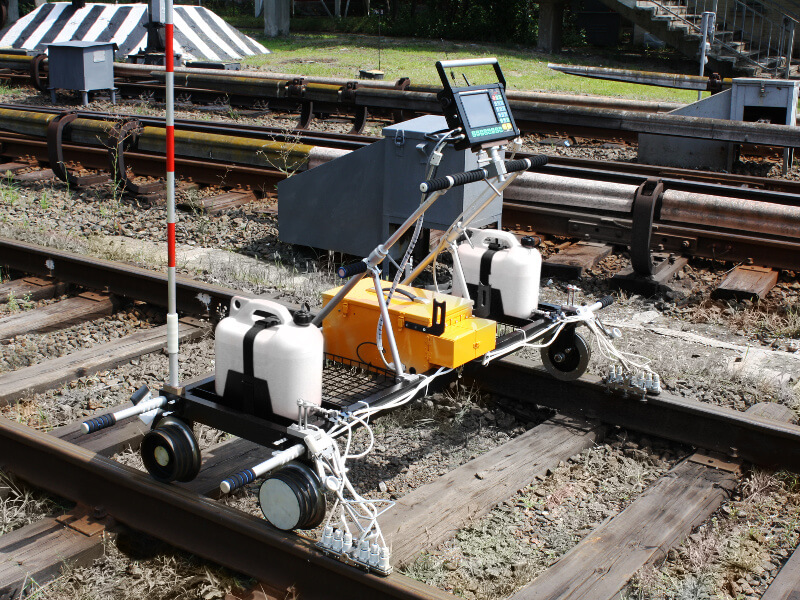
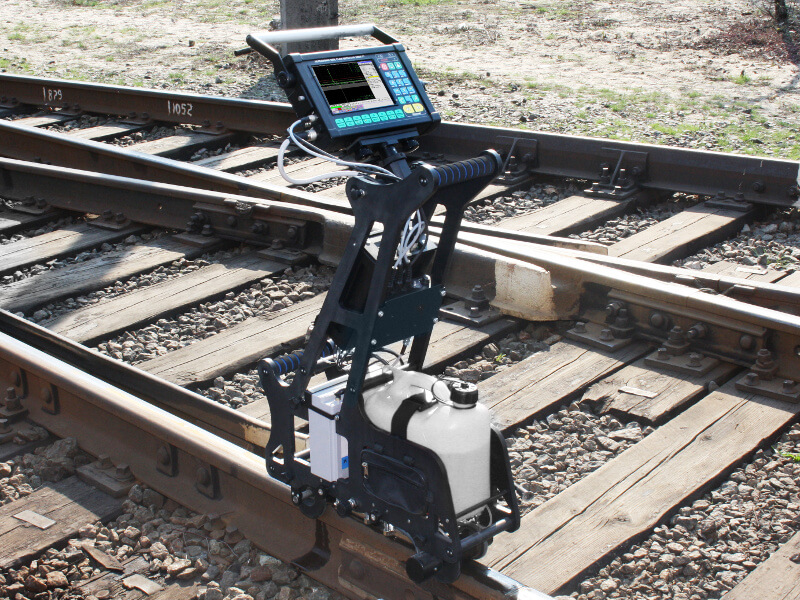
Ultrasonic Testing
Railway tracks are inspected by ultrasonic high frequency waves, usually the ultrasonic waves with a frequency of 2 to 5 MHz are used to inspect rails.
Since the defects in rails have different nature (direction of development, manufacturing defects, operational defects), different angles of ultrasound input into the rail and various sounding schemes and testing methods are used, for example: echo method, echo-shadow method, tandem methods.
Besides that, the manufacturers of ultrasonic rail testing equipment for the effective and efficient defects detection implement different types of data output to the screen, for example: A-scan, B-scan and their various combinations.
The variety of testing methods and sounding schemes, as well as various types of data visualization make it possible to effectively and with great probability detect the defects at different stages of their development.
In the rails head acting surface, as well as on the rail head running surface the quenching cracks may be developed in the process of the rails exploitation. This type of defect appears on the rail surface and develops to the depth with some time.
Timely detected and assessed defect depth in the rail head and on the head running surface allow to extend the service resource by the rail profile recovery with the grinding machines.
The eddy-current method application in this case is justified not only by a possibility to detect flaws but also by their assessment.
Manual testing of rails and welded rail connections
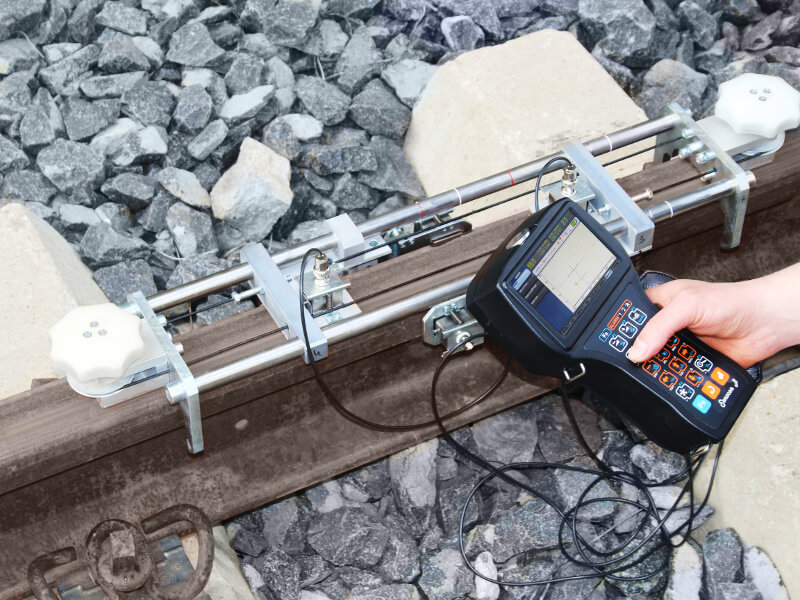
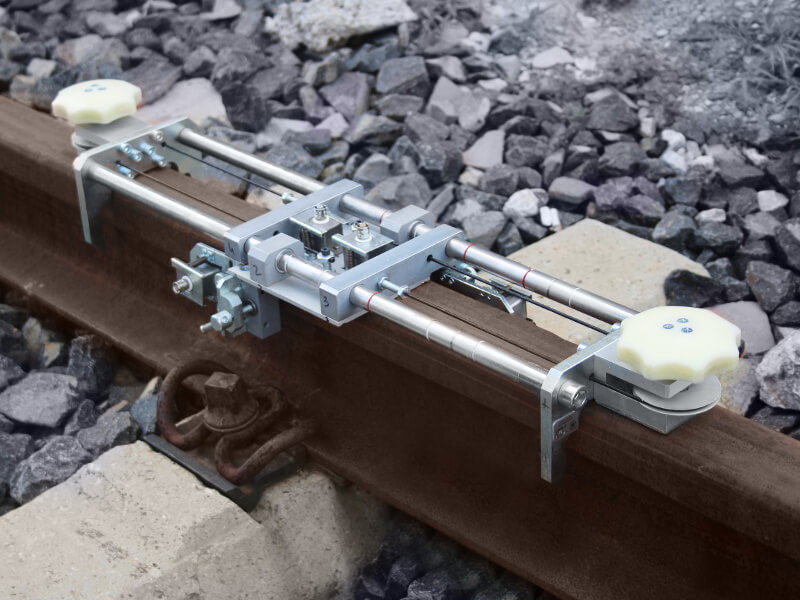
At the moment various rail testing technologies are used in ultrasonic rail inspection, which in turn require the participation of a person to interpret the results of their test. Different regions and countries apply their own approach to ultrasonic rail testing. There are three basic approaches to rail inspection:
Manual inspection and ultrasonic testing of rails implies using a hand-held ultrasonic flaw detector (Sonocon B) plus a set of ultrasonic transducers and a special scanning device (USR-01) with the help of which it is possible to carry out a secondary testing of railroad tracks laid, according to the results of mechanized inspection by ultrasonic or combined ultrasonic rail flaw detectors and flaw monitoring and detecting railcars, as well as for the pre-weld inspection of the end sections of new and used rails before welding them at rail welding enterprises or monitoring joints welded by electrocontact or aluminothermic method.
Mechanized rail testing by means of removable trolleys
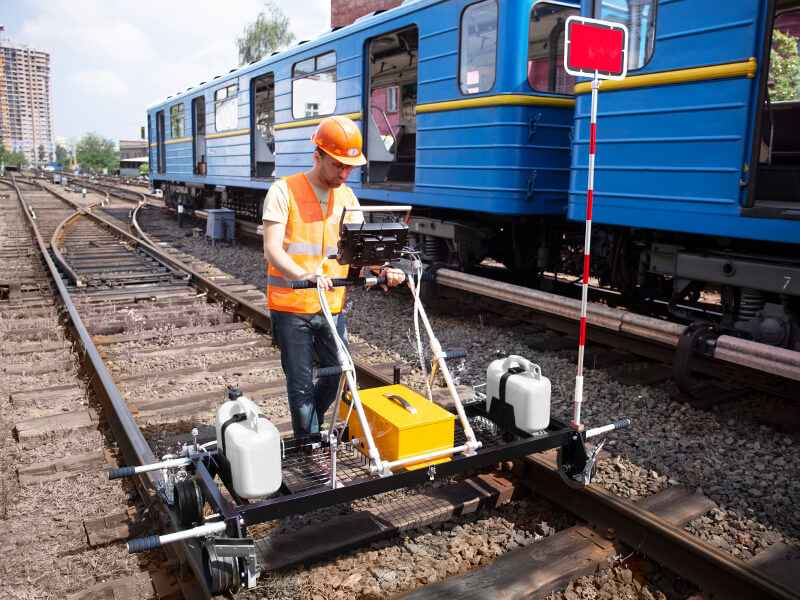
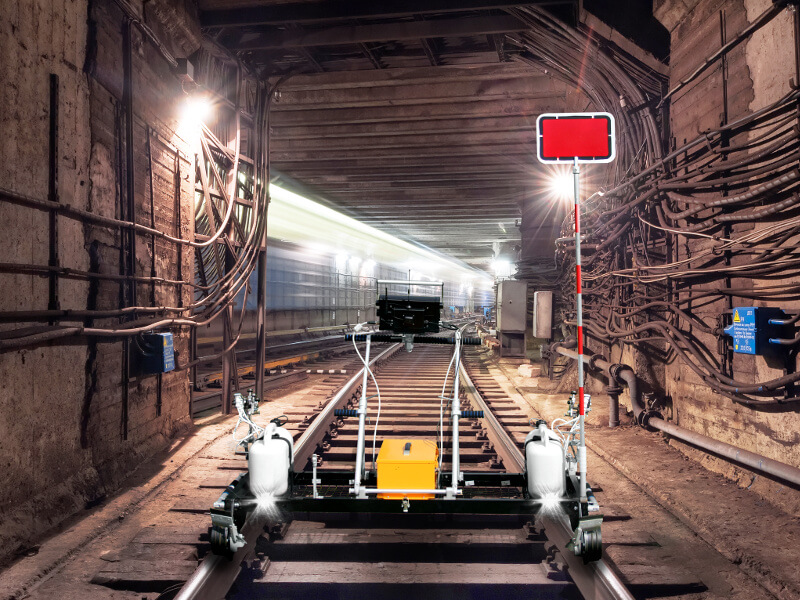
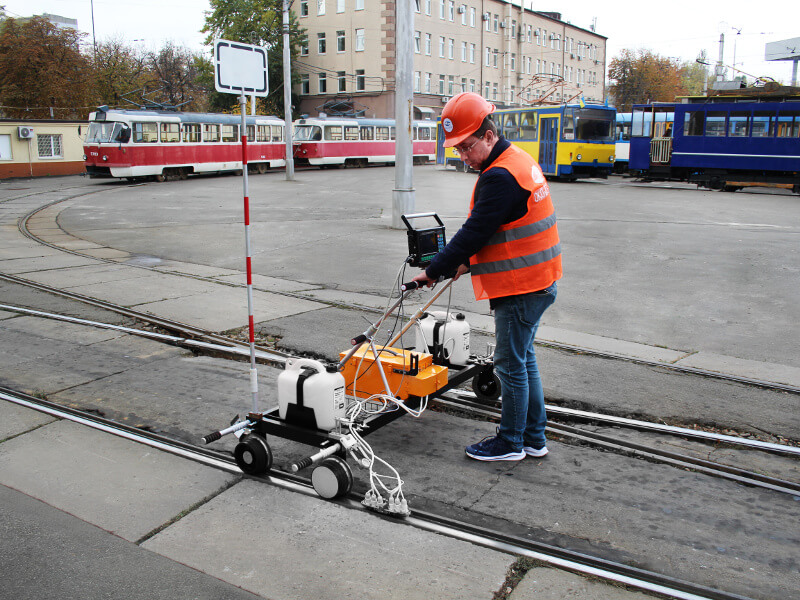
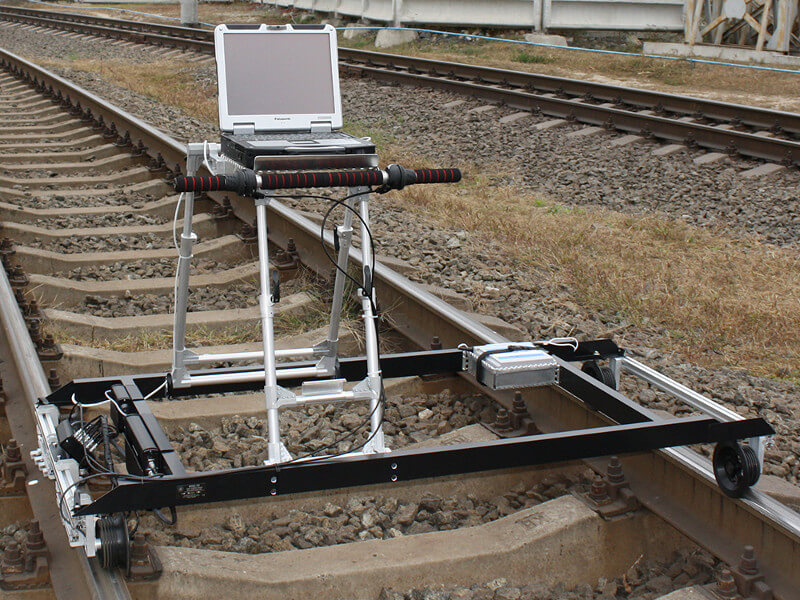
This type of testing involves the use of mechanized trolleys, which are moved by operator. There are two types of trolleys exist:
- Singlerail trolley;
- Double–rail trolley.
- Single-rail eddy-current flaw detector ETS2-77.
- OKOSCAN 73HS high-speed rails testing system
Such mechanized trolleys house the electronic equipment and transducer blocks, which in turn implement various rail inspection schemes.
Mechanized ultrasonic rail testers allow to carry out:
- Continuous monitoring at a speed of up to 4 km / h for defects in both rails of the railway track along the entire length and section of the rail, with the exception of the flanges of rail foot;
- Manual confirming testing of individual sections of rails and welds;
- Determine the parameters of detected defects and store the results of testing in energy independent memory.
Mechanized eddy-current flaw detectors allow to carry out:
- testing at a speed of up to 2.5 m/s for defects in one rail line of the railway track both on the rail head acting surface and the head running surface;
- manual prove-up testing of individual sections of the surface;
- assessment of the detected defect depth and to back up the test results in nonvolatile memory.
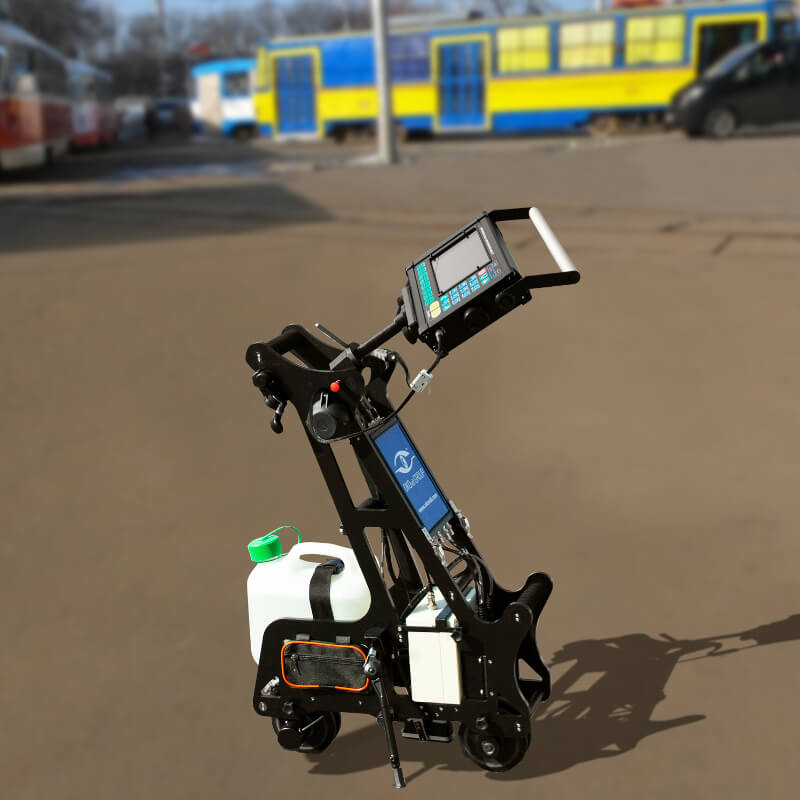
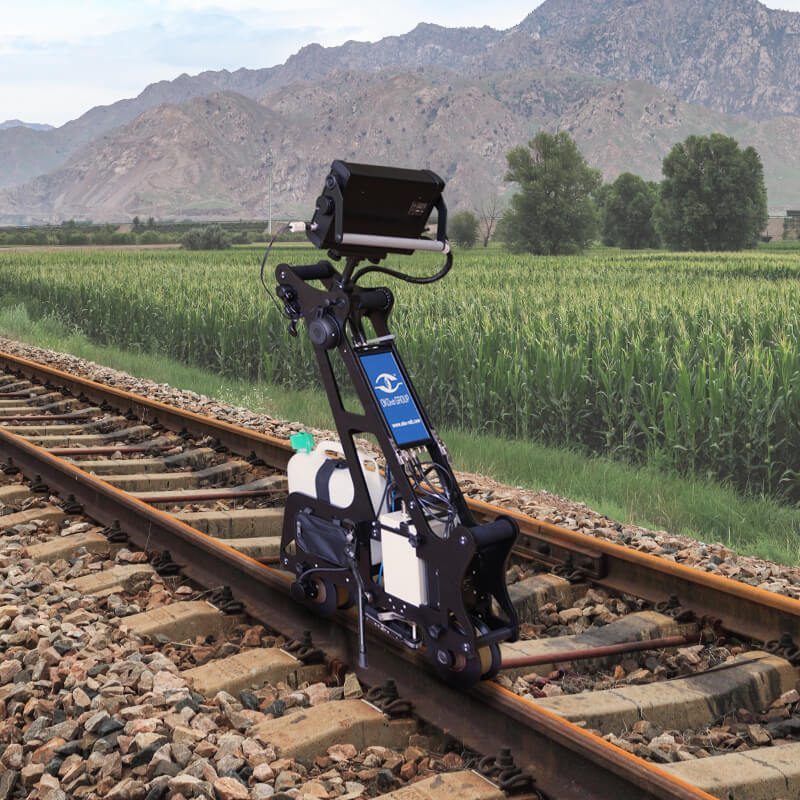
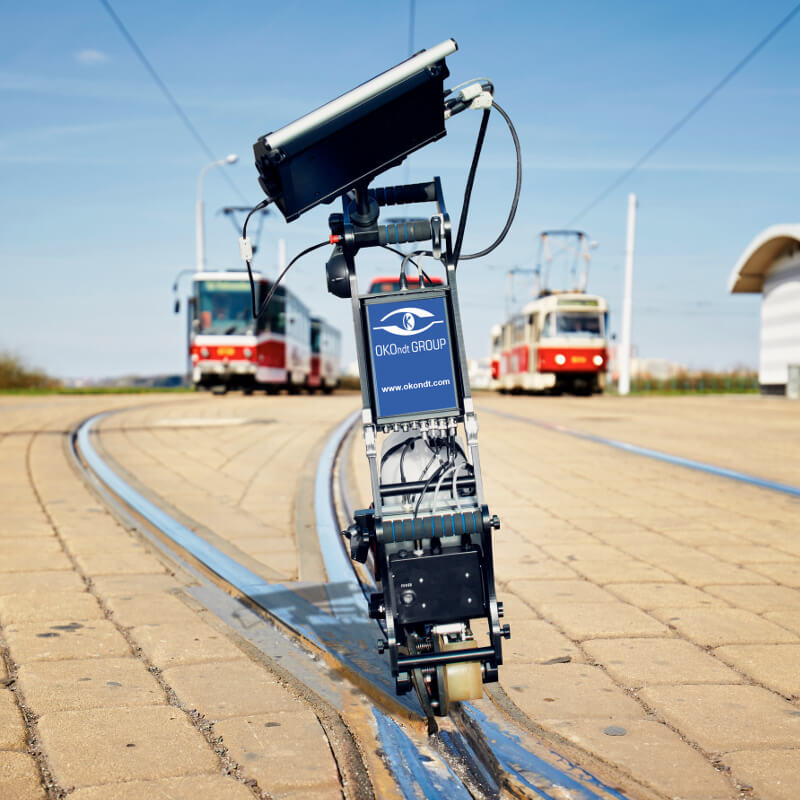
Mobile rail inspection equipment for rapid continuous testing
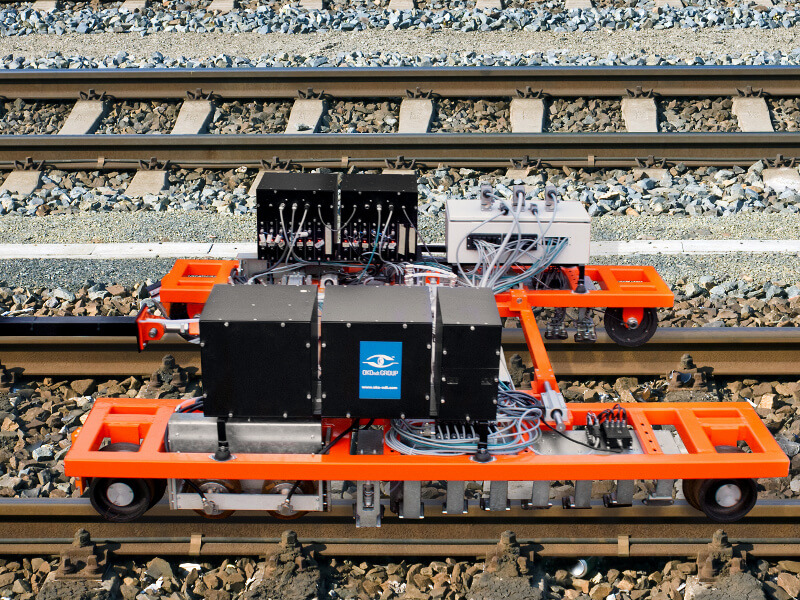
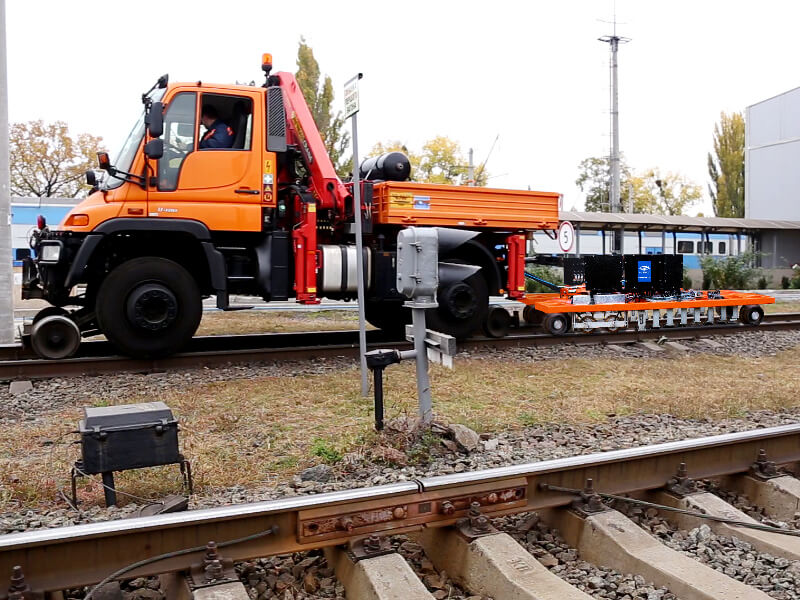
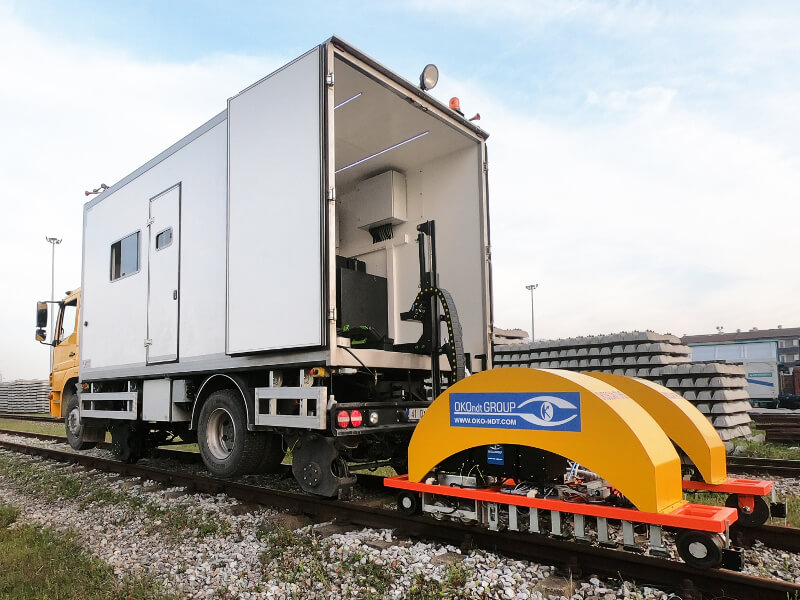
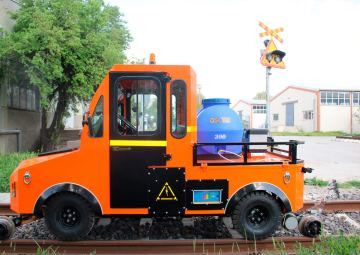
This technology lies in the fact that the ultrasonic testing of railway tracks is carried out by means of high-speed transport systems (vehicle, wagon or rail car) without stopping along the assigned route; this allows you to inspect areas exceeding 100 km per shift.
After that, the monitoring data is sent and analyzed in a remote location. Once the data has been analyzed and potentially dangerous sections of rail are revealed, the report is sent to the operators who are conducting confirmatory checks with the help of manual or mechanized flaw detectors.
OKOndt GROUP™ has specific equipment for rapid continuous testing of rails. It is OKOSCAN UT73HS - High-Speed System intended for automated rails testing at a speed of 40 km/h (25 miles) maximum. The rail ultrasonic testing unit consists of carriage, ultrasonic modules, wheel probes, software and allows to detect all types of crucial defects.
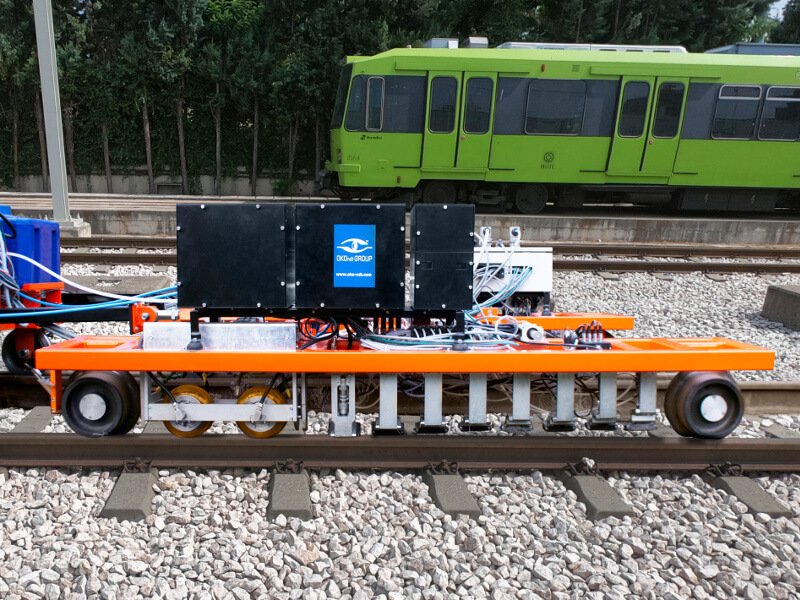
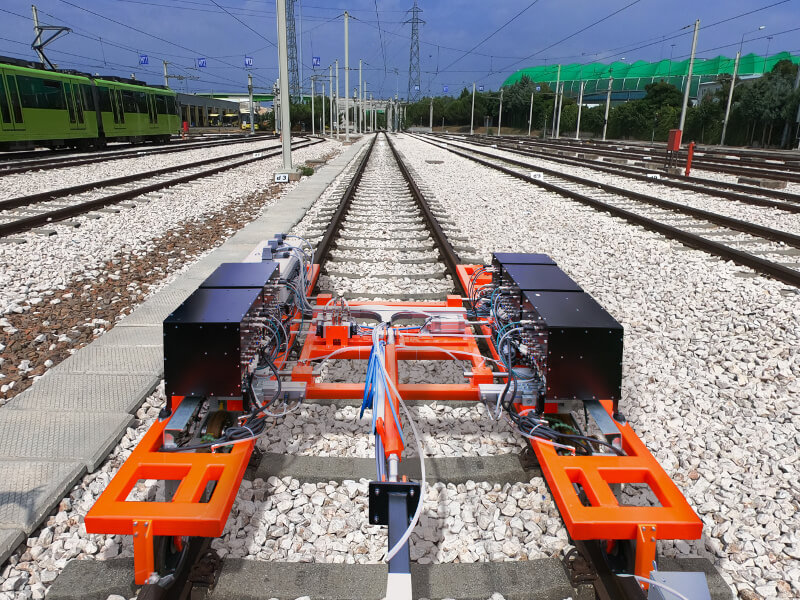